All in a Day's Work: Reporting on Occupational Health
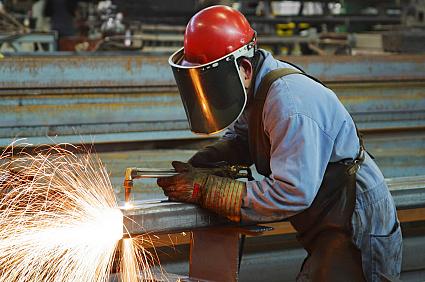
Help wanted. Pay not so great. Excellent chance of injury. Possibly fatal. No phone calls, please.
You'll never see an ad like this in the classifieds, as one of my colleagues once said, but it's a good description of many of today's positions. On an average day, 149 U.S. workers lose their lives. More than 3.9 million U.S. workers are injured on the job annually, and many more suffer from job-related illnesses. In nearly every case, these injuries and deaths are preventable.
What's behind most of these accidents? Unsafe working conditions, rather than careless workers, occupational health experts say.
This was certainly the case in my first workplace safety story, some years back, when I was looking into rumors of egregious work safety violations at a scrap metal plant near Santa Cruz, California. Most of my attempts to contact former workers failed, and the one source I developed was afraid to talk on the record. But when I traveled to the headquarters of California's Occupational Safety and Health Administration to look up records of its workplace safety investigations, I found what I was looking for.
There, in several boxes of dusty files, was a tale of 10 years of danger and dismemberment, of crippling injuries due to violations of safety standards, of worker after worker whose fingers were amputated by metal saws that lacked the required safety guards, even after repeated warnings and citations by workplace inspectors.
The inspection records were not hard to find then, and they are even easier to review today. To locate OSHA investigations of a local industry, you can simply go to its official website. Click the link "Establishment Search," then enter the name of the company you'd like to research. You can also find accident reports at "Accident Investigation Summary," also known as "Fatality and Catastrophe Summary."
OSHA and its state partners (like Cal-OSHA) are good places to begin, but there's a hitch: OSHA has suffered a series of devastating cutbacks over the past three decades and has only 1.5 inspectors for every 100,000 workers (down from three per 100,000 in 1980). According to the non-profit OMB Watch, OSHA and other government agencies conduct fewer than half the number of workplace inspections they did 30 years ago. In fact, OSHA inspectors would need an estimated 117 years to inspect all the workplaces under their jurisdiction even once -- so you may not find the records you're looking for.
Another problem is that the financially strapped agency is years behind when it comes to issuing standards for many workplace hazards, including combustible dust (see below).
Where To Find Information, Story Leads
To keep up with emerging hazards, it's a good idea to bookmark some occupational health blogs and websites, including The Pump Handle, Hazards magazine, Working Immigrants, Workers Comp Insider, LabourStart's health and safety newswire, FairWarning.org and, for more background, the late, great Confined Space blog.
And of course, don't forget to talk with people on the front lines – workers in particular. From nail salon workers exposed to formaldehyde to service and white-collar employees suffering from stress, overwork and overuse injuries from scrambling to do both their job and those of laid-off colleagues during the recession, they have a lot to tell you. The good news is that most people like to talk about their jobs. After all, some of them spend more time there than they do at home.
Also, don't neglect:
• union leaders
• employer reps
• researchers
• the labor liaison at the regional OSHA office
• the American College of Occupational and Environmental Medicine
• the Council on Occupational Safety and Health (COSH) groups, which promote workplace safety and health.
For records about the issues you're hearing about, check with OSHA, NIOSH, your state and local environmental and health departments, and other sources, and you'll have a wealth of stories to cover.
Ideas For Your Reporting
Meanwhile, here are several current issues to investigate:
Grain bin hazards: Agricultural work is often anything but bucolic. This past year, a record number of boys and men have been swallowed up by grain stored in metal silos in rural areas, and 26 of them were killed, according to a Chicago Tribune story about this little-known hazard.
Accidents often occur when workers are trying to break up wet clumps of grain. In Mount Carroll, Illinois, two teen workers were suffocated in a corn silo, and an OSHA inspection revealed the company had taken none of the recommended safety measures, such as training the teen workers, developing an emergency plan for accidents or providing them with safety harnesses.
To get started: If you work in an agricultural area, get OSHA's recommended standards for grain handling and find out whether local companies are following them. OSHA has recently stepped up its inspections of grain handling, so be sure to check the inspection records for farms in your area.
Hospital cleaning: Infection control is one of the most crucial tasks in a hospital, but more than 1.7 million people develop infections from exposure to germs in U.S. hospitals each year. Although little attention has been paid to the cleaning staff, inadequate cleaning is behind many of these outbreaks, according to assistant professor Dan Zuberi of the University of British Columbia, who has done extensive research on the topic. One reason, says Zuberi and hospital unions, is that many hospitals in the United States and Canada are now outsourcing their cleaning crews, exposing both potentially untrained contract cleaning workers and patients to the risk of life-threatening hospital-acquired infections (HAIs). In one case Zuberi looked into, an outsourced cleaning crew tried vainly to eradicate the potentially deadly germ C. difficile using a 1:1,000 percent bleach/water solution by mistake instead of the required 1:10 solution; in another, workers unable to operate a cleaning machine properly were repeatedly sprayed by aerosolized feces.
To get started: Contact local agencies working on behalf of temporary and undocumented workers, infection control specialists, hospital unions, nurses and doctors, the Los Angeles-based organization Justice for Janitors, and the Service Employees International Union, whose local chapters have held protests about the outsourcing of hospital cleaning and linked that to a rise in "superbug" infections at hospitals in Oregon and Ontario, among other places. Also check into resources from the National Healthcare Safety Network, the Joint Commission for Accreditation of Healthcare, and the agency in your state that oversees hospitals, the Committee to Prevent Infection Deaths (RID), and The Society for Healthcare Epidemiology, which offers factsheets about common HIAs. Some state health departments, including California's, have also begun releasing hospital data about hospital-acquired infections.
Combustible dust: "It's not rocket science: If you can see your footprint and write your name on the wall [in the dust], it's going to explode," one expert recently told the Associated Press, referring to flammable dust that causes deadly factory blasts - a hazard that OSHA has been looking into since 2003 but for which it still hasn't come up with a worker protection standard.
My home state of Georgia is ahead of OSHA on this one: after 14 workers were killed and dozens more injured when sugar dust caught fire and detonated an Imperial Sugar plant in Port Wentworth, the state put out emergency regulations on exploding dust. No one has been killed by combustible dust in Georgia since, but dust-related explosions continue to kill and cripple workers in other states, including six who died this year.
To get started: Dust from wood, metal, food, and chemicals is all potentially flammable. Find out whether industries in your area are vulnerable to the problem of combustible dust, and what they're doing – or not doing – about it.
Second- and third-hand cigarette smoke: Imagine a business where you have to work in a fog of cancer-causing chemicals all day long. Well, that's the case for many bar, hotel and restaurant workers in states that haven't banned indoor smoking at work. Besides secondhand smoke, they may be exposed to another hazard scientists have only recently learned more about: third-hand smoke. This is smoke that settles on surfaces like walls, clothes, and furniture, and it appears to combine with indoor air chemicals to create potent and long-lasting cancer-causing substances
To get started: Visit some smoke-heavy eating places and talk with workers, staff, and union officials about their views on secondhand smoke. Find out whether there are antismoking ordinances in the works, and interview researchers who've done research on changes in bar and restaurant workers' health in states where antismoking laws were enacted. In fact, the Robert Wood Johnson Foundation, whose mission is to improve U.S. health and healthcare, has created a handy interactive tobacco map to bring you the latest in smoking laws across the country.
Assembly-line hazards: Unless you live in the country, you're likely to have light or heavy industry in your area. If these companies involve assembly lines, the work may be both dirty and dangerous. In 2005, almost 100 years after Upton Sinclair's classic book The Jungle exposed the horrors of the nascent meatpacking industry, Human Rights Watch investigated U.S. meat packing plants and concluded that the working conditions were so appalling that they violated basic human and worker rights. Other assembly-line workers risk amputation and death from heavy, fast-moving machinery. Overuse injuries such as tendinitis and carpal tunnel syndrome continue to plague chicken pluckers, postal workers, auto workers, and others on the line.
To get started: Check out key federal safety guidelines for the industry you're looking into, OSHA inspections, and personal injury lawsuits filed against the company. You may also get story ideas by talking with employees, union health officials or your local COSH group, which often have extensive contacts among local factory workers.
Mining: Mining is still one of the world's most dangerous industries, as recent headlines remind us. In 2010, the most common causes of coal mining deaths were ignition and explosions, followed by roof cave-ins and accident involving railcars and other hauling equipment. Last April, more than 25 coal miners in West Virginia died in the worst U.S. mining disaster in a quarter-century after an enormous explosion rocked a mine that the year before had been cited for 458 safety violations. Three months later, 33 Chilean miners in a copper-gold mine were trapped 2,300 feet below the ground for a record 69 days before their triumphant rescue. By reporting on dangerous working conditions, reporters may help bring about changes that forestall future disasters in the making.
To get started: Check out inspection records at the Mining Safety and Health Administration and talk with miners, United Mine Workers and employer representatives, and occupational health specialists about what's being done to prevent explosions, roof cave-ins and other hazards.
An unexpected turn
It comes as no surprise that companies which endanger their workers often have questionable dealings in other areas. That is likely why my story on the scrap metal plant with the terrible safety record took an unexpected turn after the first installment was published. Someone called me at my paper to drop a bombshell: the same scrap metal plant was illegally processing hazardous waste for PG&E, one of California's largest utilities.
Although the transport and handling of hazardous waste is supposed to be handled only by specialized companies with trained workers dressed in what look like spacesuits, PG&E was sending old transformers filled with a hazardous chemical compound known as polychlorinated biphenyls, or PCBs, to be unloaded and drained into drums by workers with no protective clothing or knowledge of what they were handling. The utility then shipped the PCB-laced oil back up to its power plants to be burned, exposing nearby residents to byproducts that included extremely toxic substances such as dioxin. And my source had the records – including a stack of shipping manifests - to prove it.
Neither PG&E nor the scrap metal company had sought the permits California requires for hauling hazardous PCB waste. Nor had PG&E obtained an EPA permit to burn the stuff. After I began reporting on PG&E's dealings with the backwater scrap metal plant and the story appeared in California magazine, the district attorney of Santa Cruz successfully sued the utility for damages.
The outcome was gratifying. But no matter how a story unfolds, a safe and healthy workplace is a basic human right. In the best possible scenario, reporting on workplace safety can further that elusive goal.